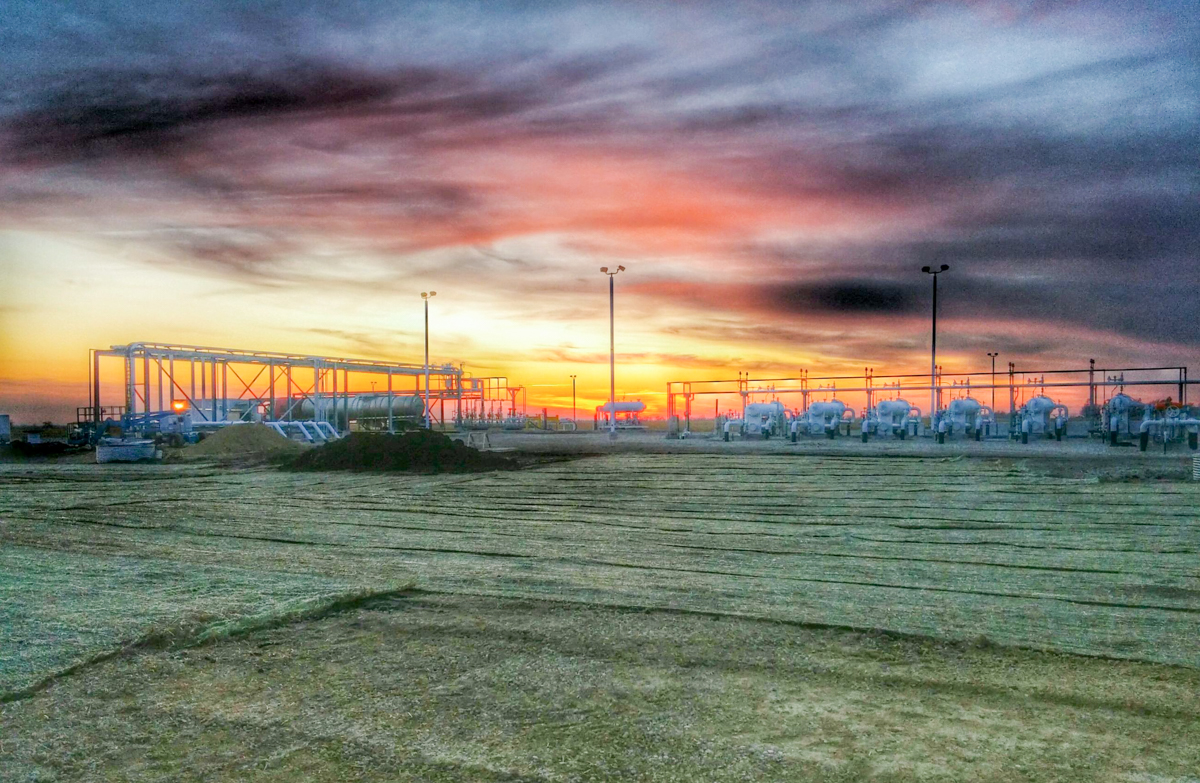
Answering the Call for a Regional NGL Facility
September 11, 2020
In his classic book on leadership, “Good to Great,” Jim Collins writes, “People are not your most important asset. The right people are.”
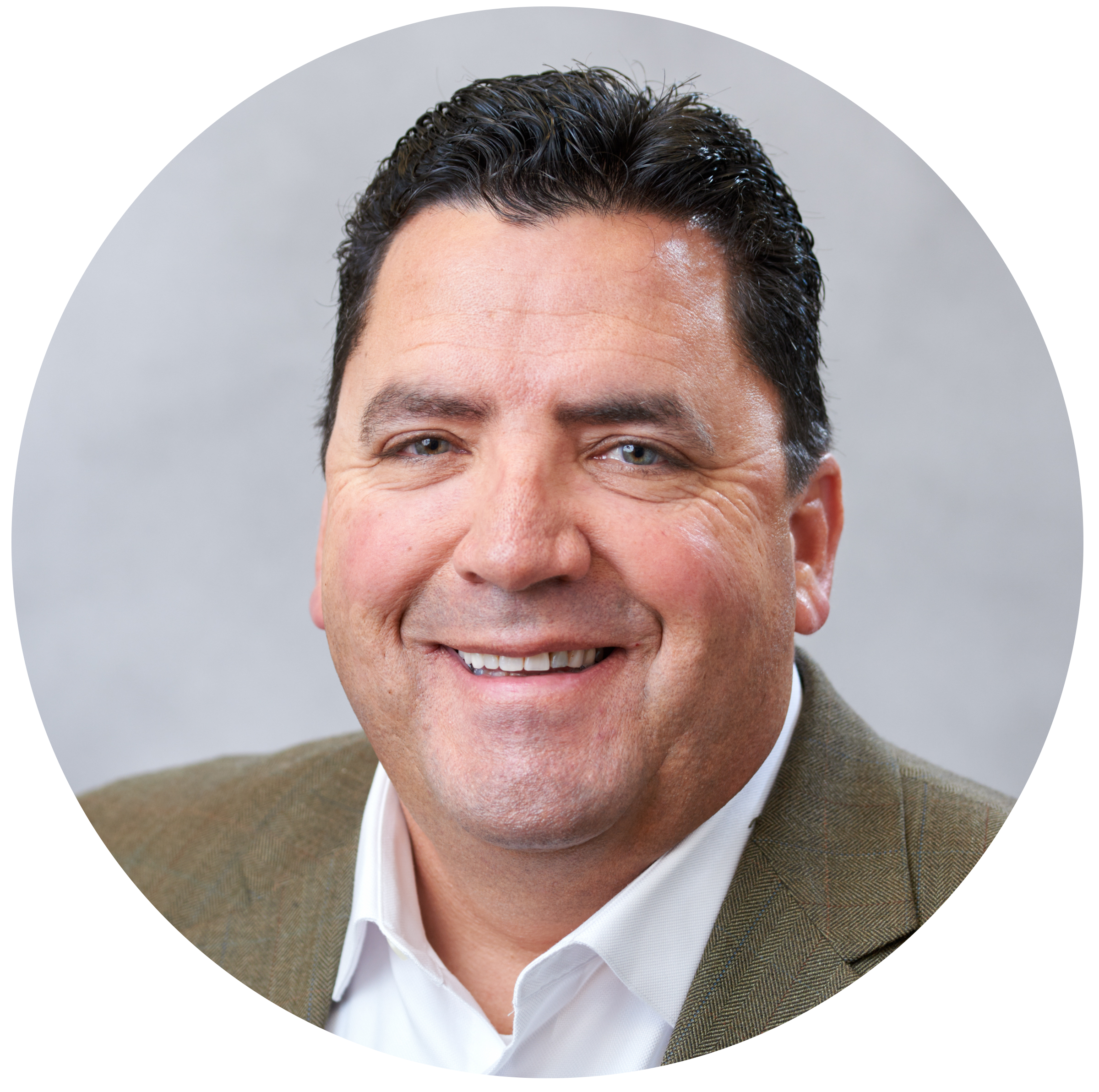
For more than a decade we’ve delivered close to 200 separate projects and studies for a regional client at their NGL facilities in Conway, Mitchell and Hutchinson, Kansas. We recently sat down with one of those right people, MKEC’s Billy Therrell, Senior Project Manager and Piping Designer, who has been working with our client nearly every step of the way, for a look back at how it all began.
Starting small
As most relationships do, ours with our client – which builds and operates facilities that store and move energy resources across the country – started out small. We began our first project with them, designing platforms for a large vessel, in 2006. Although that project was shelved due to other, more pressing needs, our partnership continued to evolve.
Two years later we dove into a major rail rack expansion, designing a new rail spur and rail car loading /Unloading rack at Conway. This was the first rail project we’d ever done – and since that time, we’ve broadened our expertise and delivered many similar projects to a variety of clients.
Manifold system
We kept busy over the next several months with smaller projects, and in 2009-2010 work on a $10 million manifold system at Conway got underway.
The new system needed to be able to receive or deliver several different types of (NGL’s) natural gas products to pipelines, trucks, rail and underground cavern storage. Our client uses brine water injection into underground salt caverns to supply various stored NGL/LPG products throughout their delivery system. Our design included five product pumps, product filters and custody transfer metering systems to displace the product into 6” pipes in the manifold system before moving on to rail cars, pipeline systems or trucks.
The goal was to segregate the products, ensure minimal cross-contamination, maintain product specification and provide accurate measurement for delivery both to and from customers. In addition to the ability to route each customer pipeline to massive underground storage caverns, we configured the distribution manifold piping with headers for nine different liquefied petroleum gas (LPG) and gasoline products. The distribution manifold our team designed can receive product from multiple pipelines while simultaneously delivering to caverns for storage or to another customer by way of truck, pipeline and rail loading. Our team also helped them come up with a way to combine the manifold system into a single area for maximum efficiency.
From expanding the truck dock in 2011 to replacing the dehydration towers in 2012 and myriad projects since, MKEC’s entire multidisciplined team of professionals has touched almost every inch of the sprawling facilities in Kansas. We’re currently working to upgrade a propane truck and railcar loading system from a 150# class system to a 300# class system, enabling higher pressure and higher flow rate, which will allow our client to load rail cars and trucks faster and more efficiently.
As MKEC has grown in size and depth of expertise, so has our relationship with our client. “When they have a problem, it makes a big difference that they know they can call us,” says Therrell. “Most times we can be there in an hour. If they call bigger firms, it’s going to be two weeks.” Therrell chalks up this longstanding client partnership to this: years of tackling the hard projects, delivering on our promises, and perhaps most important, answering the call.
Here’s how MKEC’s multidisciplined team has contributed to the engineering success on each of the projects at this regional NGL facility:
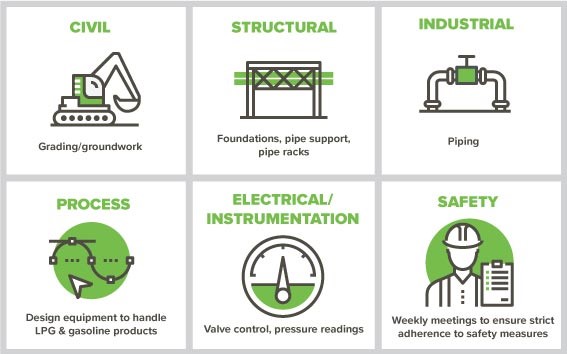
Drawing on our wide range of engineering expertise – we’ve earned a reputation as an established firm serving industrial clients and more nationwide. Ready to partner with us?