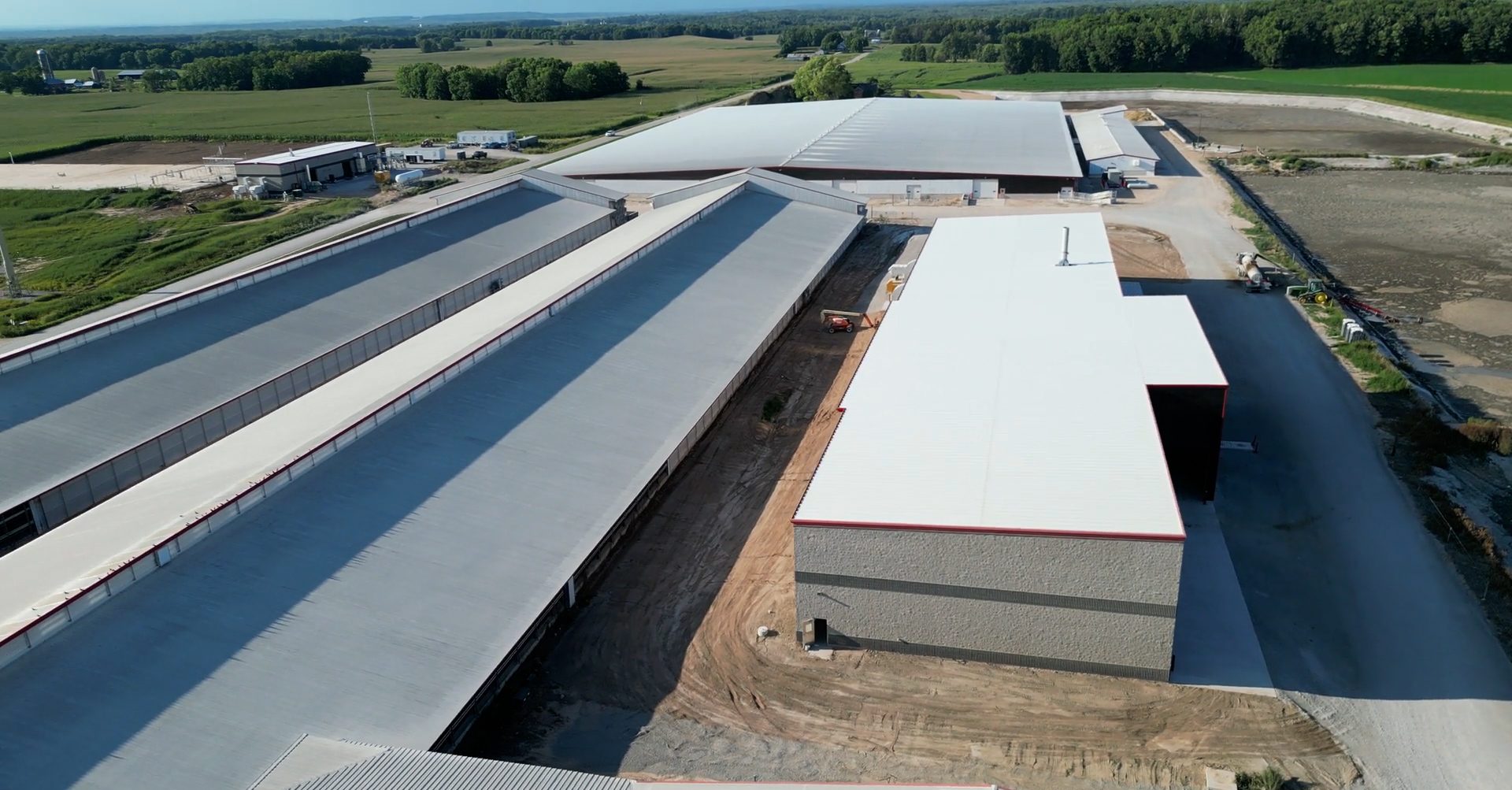
Holy Cow: Turning Manure into Renewable Natural Gas
October 21, 2024
Renewable energy is a hot topic, and at MKEC, we’ve worked on everything from wind farms to solar farms to renewable natural gas. Our latest project took us to one of the largest dairy farms in Wisconsin, where we put our skills to work to help turn cow manure into renewable natural gas.
“We had to develop how they were going to move the manure from the cow barns (holding several thousand cows) to a collection tank in a brand-new manure separation building,” said Mark Koontz, senior process engineer at MKEC. “There’s a whole system we designed to do that consisting of pumps, pits, mixers, and buried lines to move the manure into the new digester. Then we had to take the digested manure (or digestate) out of the digester and pump it back to the manure separation building where filtrate water could be extracted (via screw presses.) The resulting solids or fiber could be further processed into bedding material for the cows. The farmer was able to recover and reuse this material instead of just dumping it into a lagoon like he was doing previously.”
In addition, MKEC was tasked with designing the system required to clean up the biogas produced by the digester to turn it into renewable natural gas.
“The newer portion of what we did and the whole point of this was putting in a digester to generate biogas,” Koontz said. “It’s a mixture of methane and CO2. We had to design the whole system to take that gas and compress it and clean it up, so that we ended up with a nearly pure methane product that is injected into a natural gas pipeline.”
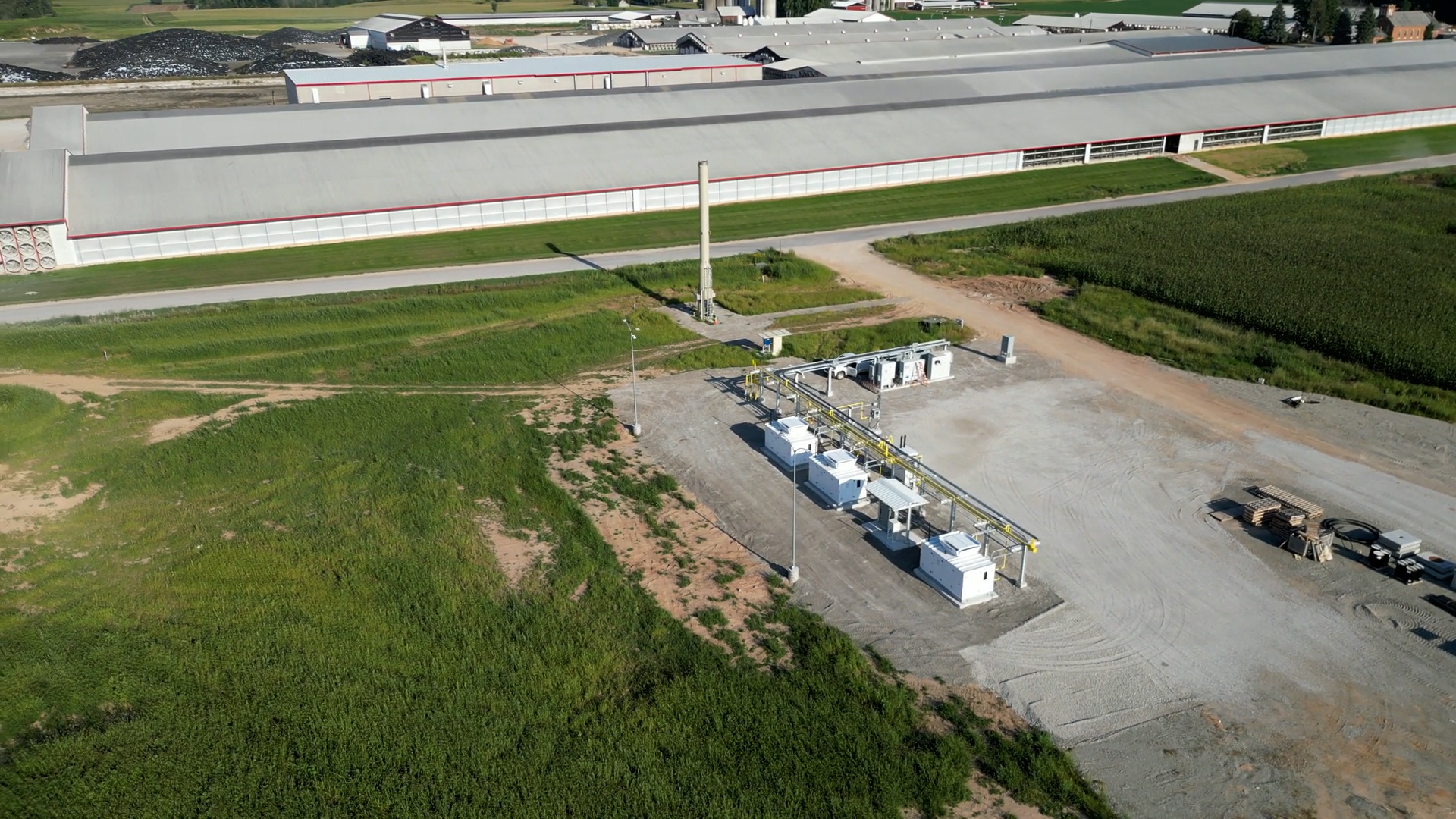
Unique challenges
Like any project, the dairy farm project came with its own challenges, the most important one being safely dealing with the toxic biogas the digester produced before it was cleaned up and turned into methane.
“The hydrogen sulfide or H2S content of the biogas produced from the digester can be as high as 4,000 parts per million,” said Travis Solomon, senior project manager for MKEC. “One hundred parts per million is considered by OSHA as immediately dangerous to life and health, so this was an eye opener for all of us working on the project.”
With the toxic gas created by the digester and the inherent risks of the gas collecting in pump pits and buildings where workers would be, caused us to pay close attention to the design details in those spaces to make them safe.
“I think our team’s experience and background with refinery projects where H2S is a known hazard gave us insight into how to deal with those hazards which included appropriate ventilation systems, gas detectors with alarm horns and lights, emergency shutdown valves, etc.,” said Solomon.
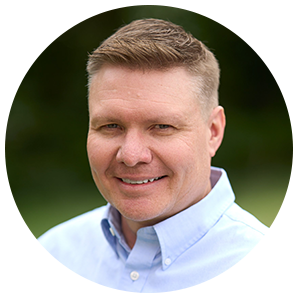
“I think our team’s experience and background with refinery projects where H2S is a known hazard gave us insight into how to deal with those hazards…”
Travis Solomon, Senior Project Manager, Mechanical Engineer
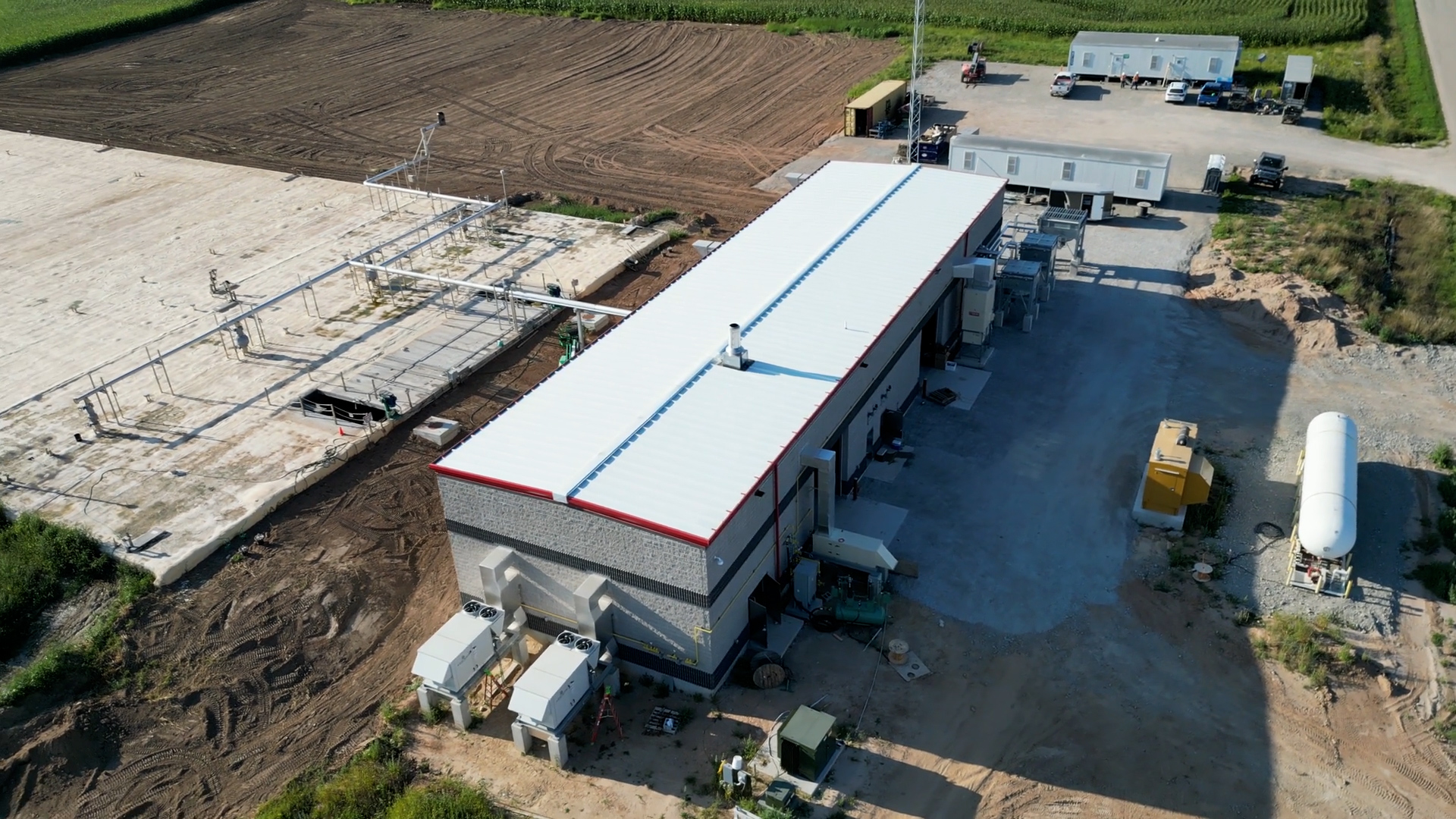
Experience matters
While this was our first time working with a dairy farm, it was not the first time we had dealt with digesters, and that experience helped the MKEC team provide the best solution for the farm.
“We’ve dealt with digesters in municipal worlds, mostly with wastewater facilities,” said Steve Adams, vice president at MKEC. “But typically, they don’t try to recover the gas. The simplest process is you burn it. You can take the gas, sort of clean it and put it into a natural gas engine and power generator that generates electricity. Then you either export that or use that, and that’s what most people do. This time we had to clean it all the way up to pipeline standards, so that they could put it in a pipeline and send it off to the utility and make money due to the high price that people are willing to pay for renewable natural gas.”
We also put to work our experience with other types of equipment to create an efficient system for the client. We involved nearly every part of MKEC in this project, including process, mechanical, electrical, civil, instrumentation and controls, and structural. Our broad expertise helped to make the project successful.
“This project involved new buildings, pumps, tanks, mixers, piping systems, electrical and control systems — all things that we have experience with in design. We were able to put together a realistic 3D model of the facility and hold several key design reviews with not only the Owners and investors but also the farmer and his staff. I think that really helped them to see what was being designed (and ultimately built) and gave them the opportunity to provide meaningful feedback to us,” said Solomon.

Learning something new
As much experience as we have in all facets of engineering, though, we sometimes run into areas of a project where we need some help. And that was true on this project.
“One area that we probably don’t deal with as much, but was required as part of this project, was solids conveying,” Solomon said. “The process of making the bedding involved the use of screw presses, a large rotary drum dryer, and several conveyors (both screw augers and belts). This kind of equipment isn’t something our team deals with very often.”
When our team doesn’t know a lot about something, we often rely on our vendor partners to help educate us.
“Generally speaking, vendors are very helpful,” Solomon said. “We understand the physical properties of the fluid or product and what flow rates we need to move. We understand the constraints of the space or building in this case. They can give us drawings of their equipment, and we can model it to know how it’s going to fit. They can also provide us with other important details such as equipment support requirements, motor horsepower requirements, etc. The vendor helps supply a lot of the information that we wouldn’t necessarily have in house.”
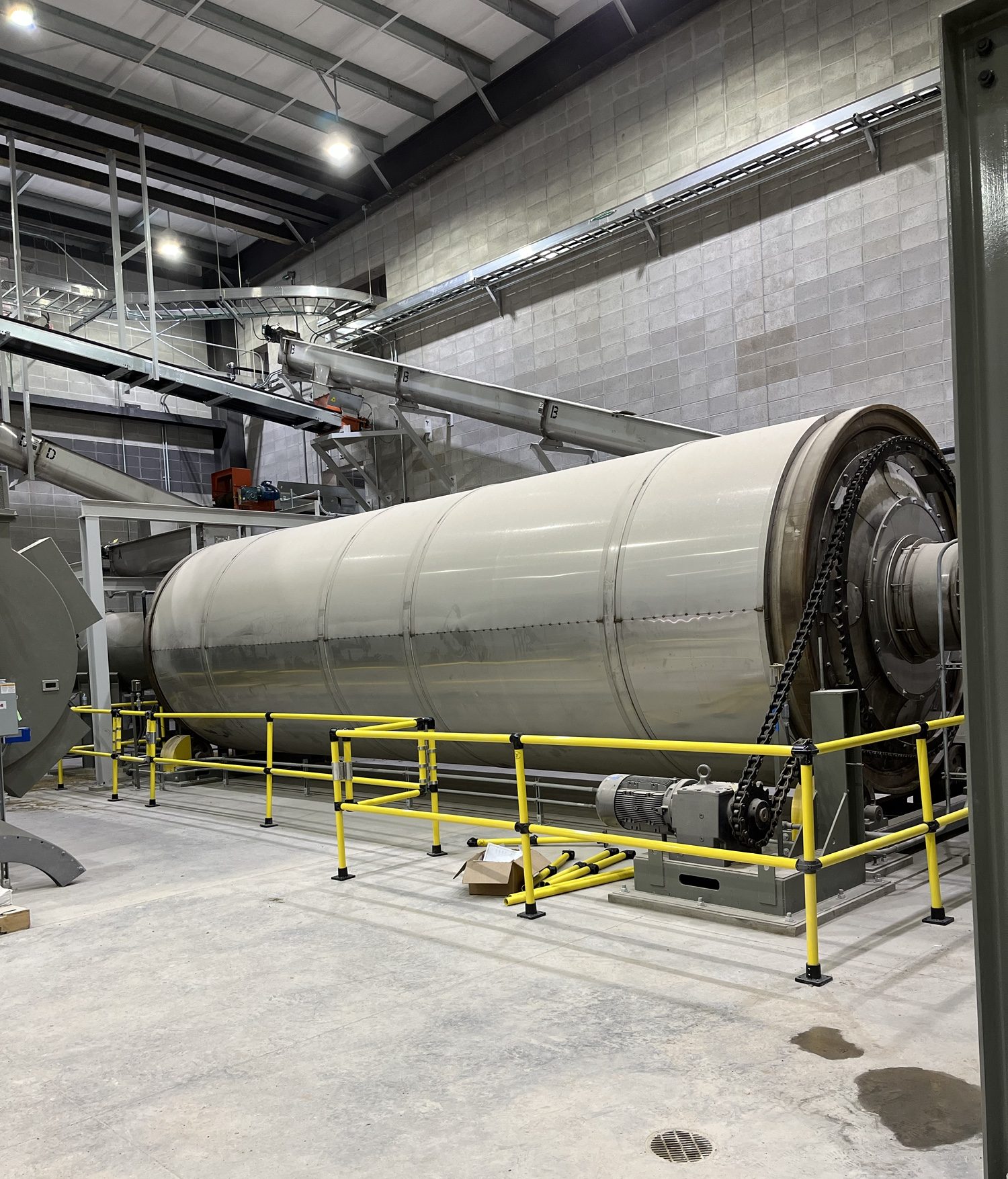
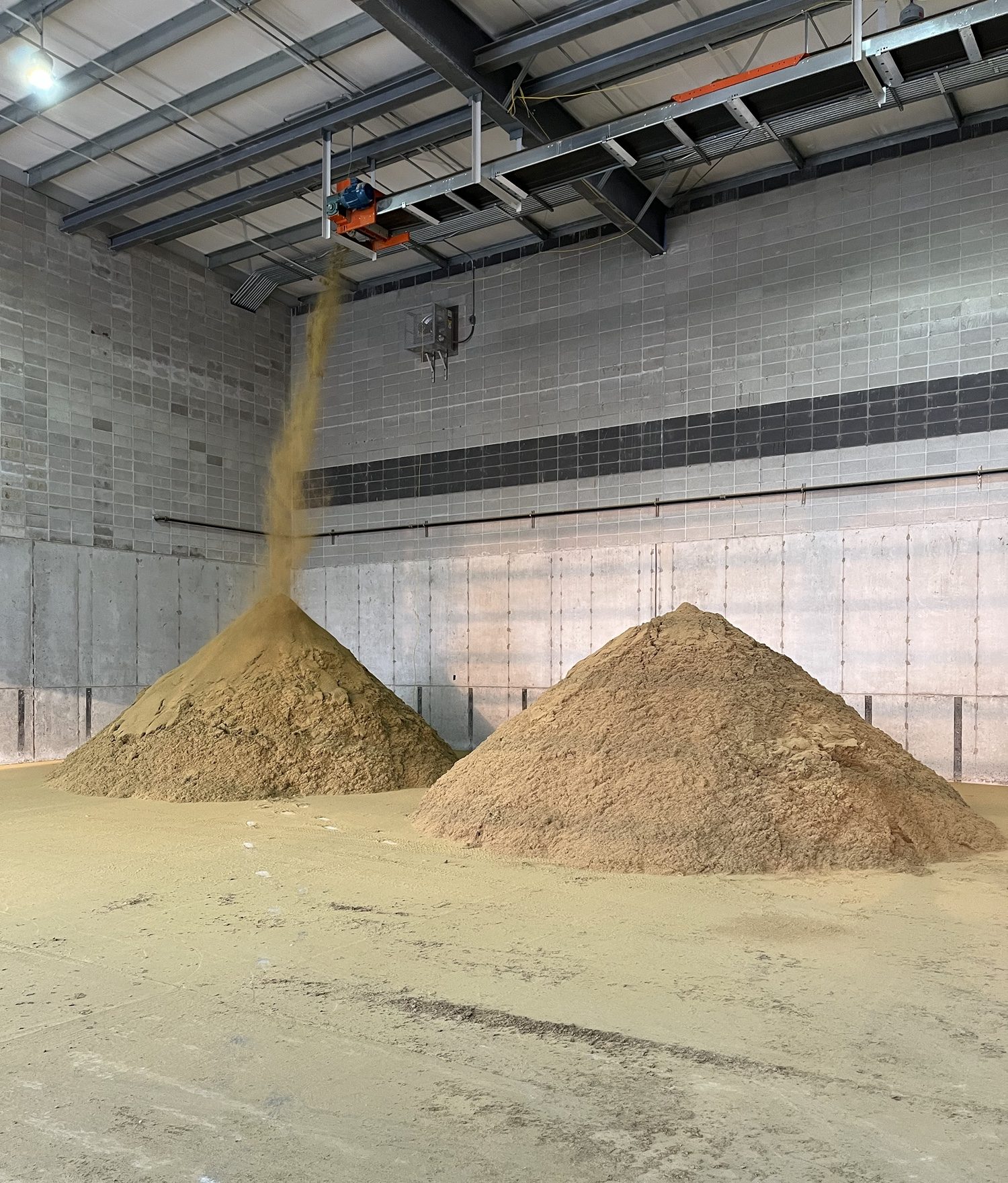
Helping the environment
One of the benefits of a project like this for the client is to recycle a product that would otherwise simply go to waste. Because of government tax credits and financing from investors that make a project like this viable, MKEC was able to get involved and help create a system that turns manure into renewable natural gas and bedding the farmer can use for his cows, which both protects the environment and saves him money.
“In the long run it’s great for the environment,” said Don Crawford, controls engineer for MKEC. “Methane gas that would have just gone up and mixed with our air, can instead be captured as a source of energy. The resulting solids product from the process is used as a bedding material that can be used in the same buildings it came from or even sold to other area farms. There are a lot of benefits to this process compared to spreading the manure on fields or piping it to a lagoon.”
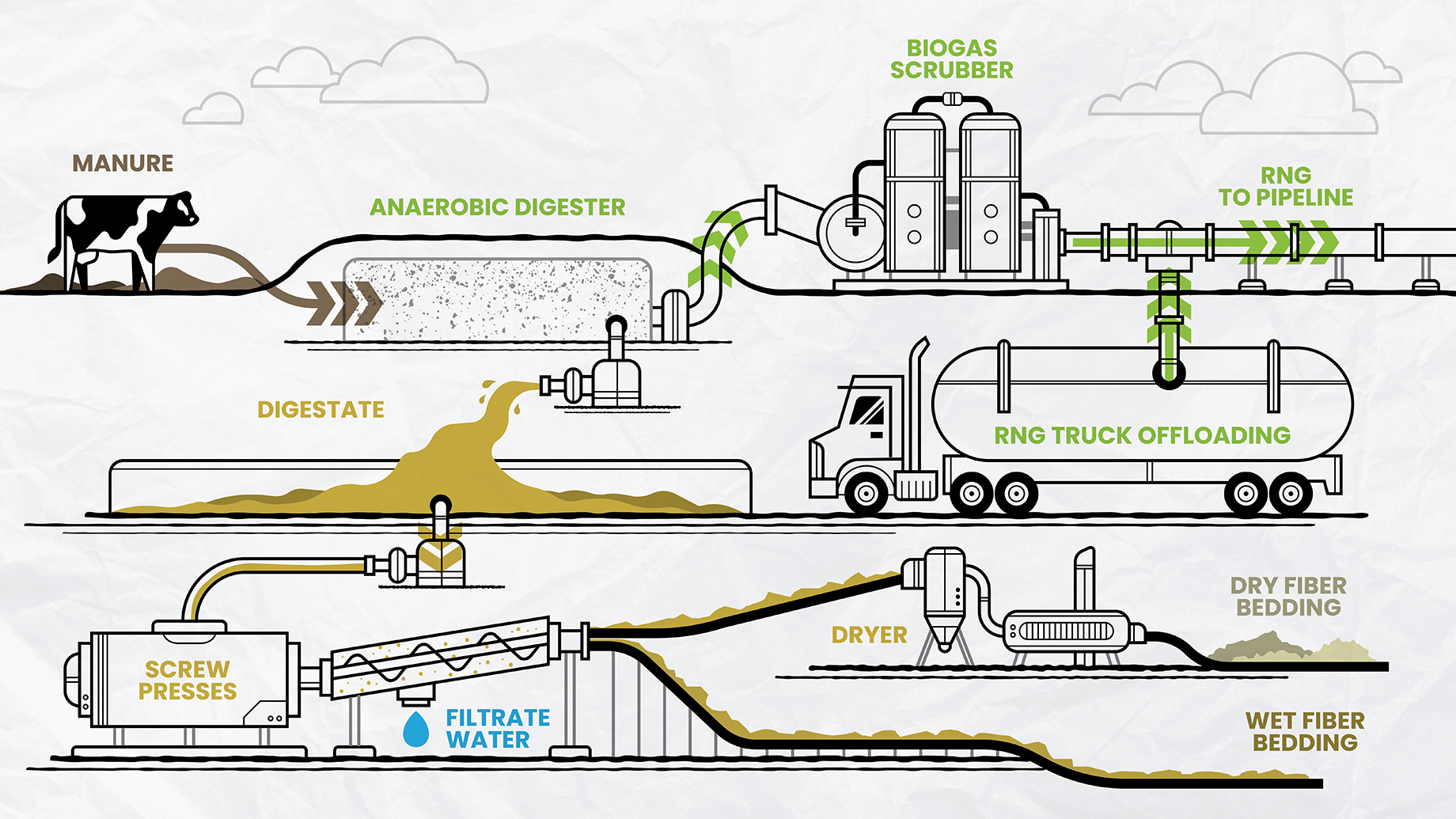