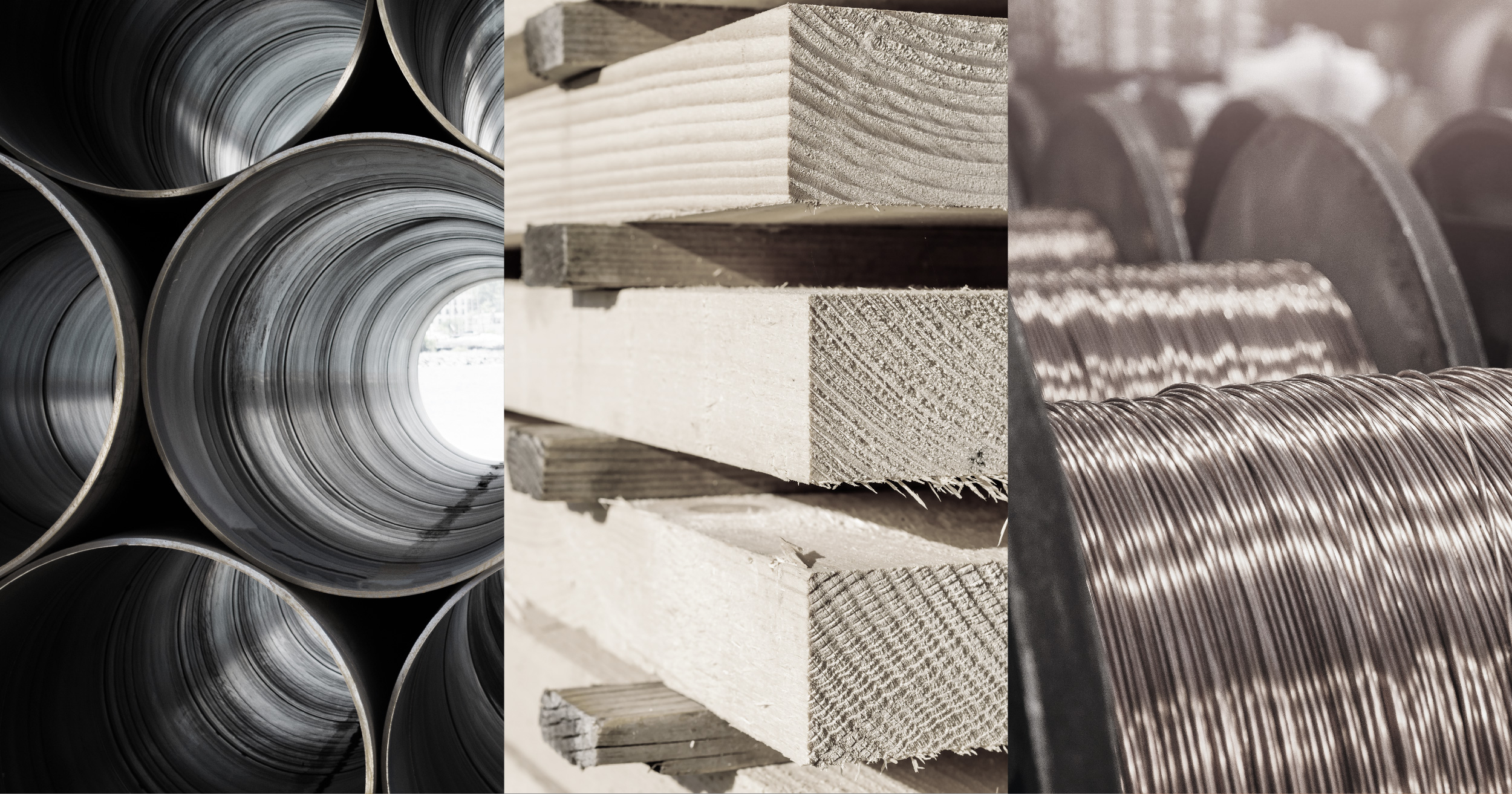
Putting Company Values to Work to Deal with Supply Chain Shortages
May 12, 2022
You can see it on your store shelves and hear about it in the news. Supply chain issues are everywhere, including the architectural, engineering, and construction (AEC) industry.
The combination of just-in-time production, a global supply chain, a pandemic and now a war in Ukraine have stretched the supply chain to the breaking point, resulting in shortages and higher prices.
And that brings new challenges to engineering projects. Fortunately, our core company values of trust, integrity, humility, responsibility, and mutual respect have prepared us to confidently deal with this new challenge while still providing our clients with the quality work they deserve.
Why are there shortages of materials?
It would be easy to blame material shortages on the pandemic, but the truth is a variety of issues converged with the pandemic to create supply chain backlogs.
The trend toward just-in-time production means many manufacturers don’t keep a huge stockpile of key components they need to make their goods. They rely on the supply chain working like a well-oiled machine to keep parts moving through the system.
Pandemic shutdowns in key manufacturing areas put a kink in that just-in-time system, causing manufacturers, wholesalers, and retailers to end up with shortages.
Exacerbating the delays caused by pandemic lockdowns is a shortage of truck drivers in the United States. As more and more production moved to the Far East, container ships have gotten larger and larger.
In fact, many container ships are now too large to use the Panama Canal, which means that the cheapest way to move goods to the United States is to ship them to a West Coast port and truck them overland to the rest of the country.
These West Coast ports are struggling to unload container ships because there aren’t enough trucks for all the goods coming into the country.
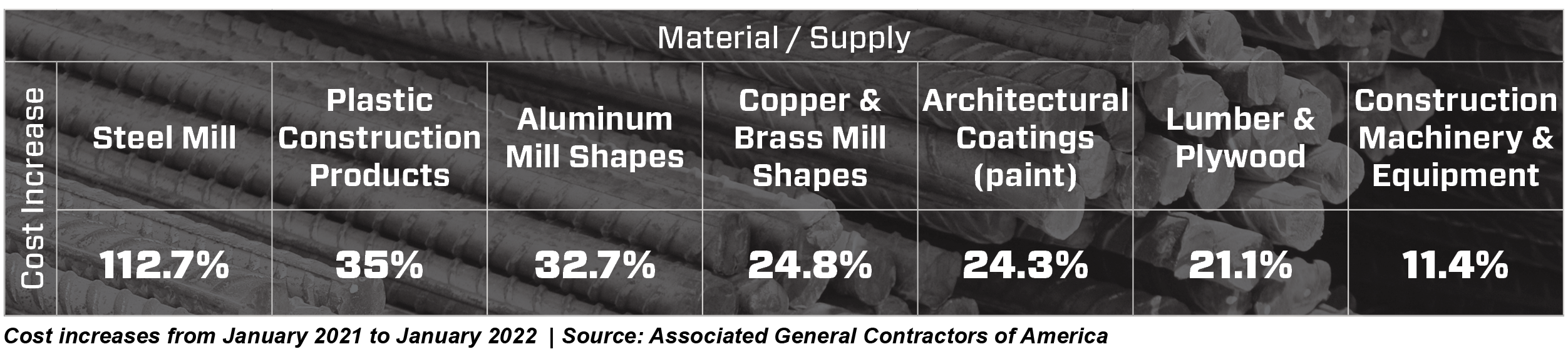
What does this mean for the AEC industry?
Shortages have affected everything from cars to toilet paper, and building materials are no exception. Materials that we once expected to simply be available may not be, which means everyone in the industry has to be ready to make changes either in the timeline, the budget or the materials being used. It takes creativity and flexibility on everyone’s part to keep projects on track.
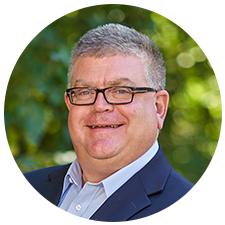
“During construction, I’m running into contractors not being able to come up with materials and delaying projects. It’s something that’s out there, and that’s something that we have to deal with.”
Jay Anglemyer, PE, Civil Engineer
And the concern about delays in industrial projects is changing the way we design projects.
“We are having to pay close attention to delivery times and design accordingly,” says Graham Lingg, an MKEC mechanical engineer. “We may need to look for ways to be more creative and design ways for components to be installed post-startup if they cannot arrive in time. The biggest delays are seen in special metallurgies specifically those containing nickel.”
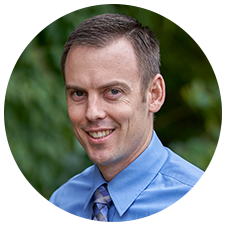
“We may need to look for ways to be more creative and design ways for components to be installed post-startup if they cannot arrive in time.”
Graham Lingg, PE, Mechanical Engineer
How is MKEC handling supply shortages?
Our first priority is maintaining the trust of our clients. Supply shortages can be frustrating and cause delays. No one wants to bust through deadlines or go over budget. We view it as our responsibility to get projects done on time and on budget.
When we discover supply chain issues are going to impact a project, we treat our clients with respect. We share the issues with them and work together to find a solution.
That may mean that we choose a different material or that we change the order of work to allow for more time for the material to reach the project. No matter what solution we choose, we do it in concert with our clients, with full transparency and integrity.
“If something has to be delayed, we understand what those delays are and tell our clients what they are as we understand it,” Anglemyer says.
Whenever possible, we try to find an alternative solution.
“Usually, things have been designed for a certain standard,” says Keith Ayotte, senior project manager, municipal services for MKEC. “Either you switch the pipe, and this is acceptable, or you wait six months. A lot of our designs must be flexible.”
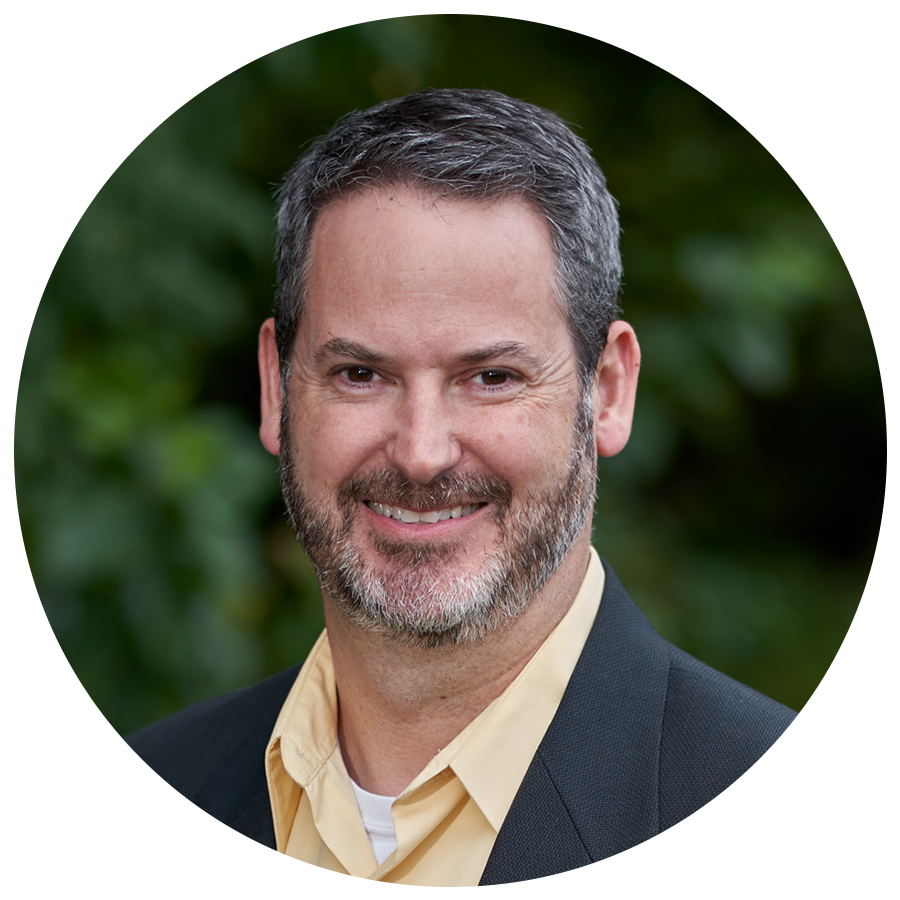
“Either you switch the pipe and this is acceptable, or you wait six months. A lot of our designs must be flexible.”
Keith Ayotte, PE, Civil Engineer
Double-checking our supply sourcing early in the project is one way we’ve adapted to the supply chain crunch. Clients are fully on board with ordering equipment and bulk material much earlier in the process to make sure those materials arrive in time.
“We’re now in the practice of asking those supply questions throughout the design process instead of waiting until the end of the design,” Ayotte says. “It has increased the interaction between engineers and suppliers. We’ve always interacted with our suppliers but not to that level. Now, even if you think it’s standard stock, you call someone and ask.”
Senior project manager Travis Solomon agrees. “Some of our clients are requesting ‘purchase ready quotes’ much earlier in the design process for commodity type items and not just major, engineered equipment. With the supply chain issues, a lot of our clients are considering purchasing these items themselves to help minimize the risk of a schedule delay. As a result, time that would have been spent later in the detailed design phase coordinating with vendors for final quotes is being pulled back earlier in that phase and in some cases even the front-end engineering phases.”
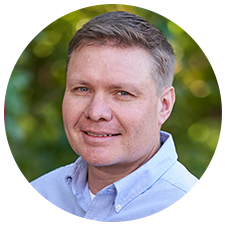
“Some of our clients are requesting ‘purchase ready quotes’ much earlier in the design process for commodity type items and not just major, engineered equipment.”
Travis Solomon, PE, Mechanical Engineer
While changing the supply chain situation is beyond our control, we do our best to mitigate the impact on our projects. And when we can’t, we’re open and honest about the situation. Because that’s who we are.